Oakham Trade Park: 2022 ProCon Leicestershire Awards Finalists!
- milliephillips3
- Sep 7, 2022
- 5 min read
#TeamWilten are delighted to announce that our recently completed Trade Park at Panniers Way, Oakham has reached the final for the 2022 ProCon Leicestershire Awards in the Large Non Residential Category!

ProCon has been connecting professionals in property and construction and celebrating the best building projects.
The ProCon Leicestershire Awards are the county's biggest celebration of the built environment and the people who develop, design and construct winning developments.
Wilten Construction were appointed as Main Contractor by Tungsten Properties for the construction of 18 nr. Industrial / trade counter units at their new trade park development in Oakham, Rutland.
The trade park is part of a wider regeneration scheme, bringing improved social and economic value to the local community. KEY FEATURES
18nr. Trade Units, complete with external works incorporating:
Enhanced Thermal Efficiency
Designed with 10% reduction of CO2 emissions
Enhanced Acoustic Performance
Sustainable Drainage Systems
EPC A rated
Maximum flexibility incorporated for occupier needs
MAIN PARTIES
Client: Tungsten Properties
Employers Agent: Goodrich Consulting LLP
Architect: HTC Architects
Engineer: PRP UK Ltd
Main Contractor: Wilten Construction
PROJECT OVERVIEW
Project Value: £4,600,000
GIA: 47,500 sqft
Start Date: September 2021
Duration: 36 weeks
Completion: June 2022
EPC Rating: A Rated
The project sits within a wider development, aimed to boost the local economy and widen the community, including a new residential development and commercial uses including a BP/M&S Petrol Filling Station, Aldi Supermarket, McDonald’s restaurant and a Marstons’ pub.

Creative approach to property development including the issues and challenges overcome:
The creative approach required careful consideration of its surroundings and close collaboration with the local planning authorities and residents to provide a development sympathetic to their needs and desired outcomes.
These challenges met were overcome through the design and construction, incorporating:
Careful selection of cladding colours to blend in with the surroundings and characteristics of the local area, not usually selected for this type of construction.
Acoustic assessments and treatments to the building elevations.
Constraints on working hours to provide minimal impact to the local community.
Good maintenance of the roads during the construction works.
Registering the site Considerate Constructors and engaging through construction with the local residents and neighbouring businesses to minimise disruption.
Design excellence:
The latest warehouse design techniques were employed to ensure delivery of market leading design and quality.
Energy Efficiency was enhanced above minimum standards by:
Achieving an EPC A Rating.
Increasing insulation values to the cladding systems.
Enabling the building for renewable energy.
Procuring materials from sustainable sources.
Wastage was minimised by:
An engineered approach to the earthworks, re-designing the external levels and site layout in the tendered design, resulting in a 4,000m3 reduction of cart aways off site, re-using in the works.
The use of composite cladding, pre-manufactured off site.
Designing out ground beams.
Construction quality and materials used:
Full height cladding to perimeter of building (mix of horizontal composite and vertical built up). Barrel vault roof (built steel cladding).
All materials used in the construction were new and high quality, source from reputable and sustainable suppliers .
Visual impact, internally and externally:
The visual impact externally was one of the biggest challenges of this project. It required sympathetic cladding colour selection to ensure it blended into the local area.
Sympathetic environmental impact and sustainable aspects:
The development incorporated sustainable drainage (permeable paving).
Sustainable techniques and materials were incorporated throughout the project.
Waste was minimised through design and 99% of waste generated on site was recycled.
Cut & fill, stabilisation methods were used to avoid the need for cut & cart (i.e. huge amounts of material going to landfill and the requirements for huge amounts of aggregate top up).
Innovation used in the development / scheme:
Innovation applied to the scheme consisted of using the latest design technics, a fully digitalised and electronic approach to document management, and applying an engineered approach to the earthworks and drainage, whilst not compromising on any visual or sustainable aspects of the project.
Integration into the surrounding area:
As above, the site sits within a wider scheme of development which includes new residential development and commercial uses including a BP/ M&S Petrol Filling Station, Aldi Supermarket, McDonald's Restaurant, and a Marstons' pub.
Visual and economical impacts were considered and the development was designed to minimise the impact on the local residents, whilst providing a big boost to the local economy with job creation and access to reputable trade businesses not previously available in the area.
Budgetary considerations / value for money:
The construction was significantly over budget following a delay to the planning permission and rising cost of materials and labour occurring during and after the COVID-19 pandemic.
Wilten Construction were engaged by the Employer to provide significant cost savings to the construction costs in order to make the scheme viable to proceed.
By applying a series of value engineered savings to the scheme, Wilten Construction were able to save 10% on the build costs to allow the project to move into construction. These included:
Engineered approach to the earthworks, removing the requirement for specialist ground improvement, and modifying the soils on site.
Re modelling the external levels to achieve a cut / fill balance on site.
Re-designing the drainage, without any impact to the original designed scheme.
Improving the design details to the steel frame, curtain walling and internal walls.
How well the development meets occupier needs:
As Jenny Clarke, Associate Development Director for Tungsten Properties, said at the beginning of the project:
Oakham has a strong market with high demand, so we're excited to get started to build these new high spec units for local and national businesses. Already, more than 60% of units are under offer to companies to let them, showing the strength of demand out there from businesses.
By Practical Completion the scheme was mostly let and / or purchased.
Project walkthrough: Tungsten Properties, New Trade Park, Oakham
As tenants came on board there were several enhancements to the design required in meeting the future fit out requirements, bespoke to the individual occupiers. These were all captured and carried out during the construction.
In meeting the occupier needs, the development incorporated:
EPC A Rated units, to meet the occupier requirements for thermally efficient buildings, especially with rising energy prices.
Good location, fully serviced by public services, with customer parking and cycle storage.
A haunch hight of 6 meters, to allow for maximum flexibility for occupier fit out potential requirements (racking and mezzanine).
Internal slabs designed for racked storage and mezzanine loads, providing maximum flexibility.
All services (electrical, gas, water and BT) brought into the units.
Level access doors and shop front glazing.
Signage zone ready.
By practical completion most trade units had been let and key occupiers, such as Howden's, commented on handover that this is one of the best sites that they have taken possession of.
The winner will be announced on Thursday 10th November 2022 at the ProCon Awards Evening, King Power Stadium #TeamWilten.
On recieving the news, Naim Basha, Director for Wilten, commented:
We are massively proud of this achievement: to see industrial development being recognised as finalists at this year’s ProCon Awards.
Space: Built to Work is Tungsten Properties mission, and this investment fully delivers. The Space created with these Trade units, benefiting from market leading design and professional expertise, are multipurpose; designed with maximum flexibility in mind and limitless potential. The investment by Tungsten Properties in this project will be realised for years to come boosting the local economy, providing job creation, and improving local amenities.
#TeamWilten #WiltenPromise #finalist #competition #ProCon #construction #loveconstruction #winningmentality #manageddesign #awesomeclientteam
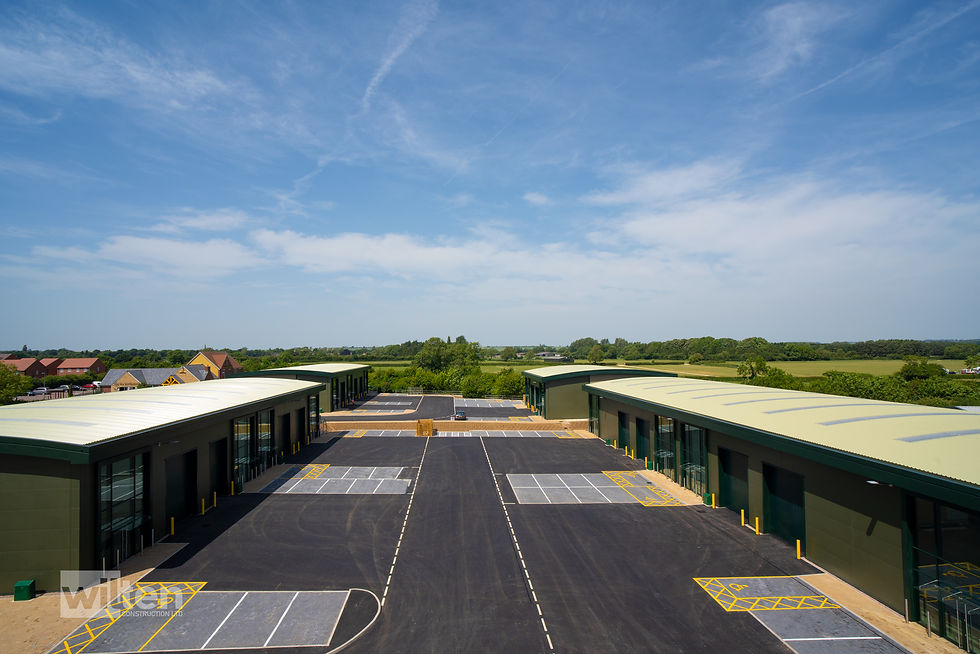
Comments